How to manufacture bras? You need to know.
What is a Bra?
A bra, or brassiere, is a specialized undergarment designed to support and cover a person’s breasts. Primarily worn by women, bras serve multiple purposes, including providing shape, comfort, and support, while accommodating a wide range of sizes to suit different body shapes. Understanding the bra manufacturing process is crucial, as it combines artistry, engineering, and a deep understanding of the human body.
Why Do We Need Bras?
The need for bras typically arises when girls start to develop breast tissue, usually around ages 10 to 15. However, some may begin this development earlier or later, depending on individual factors. Several signs indicate the necessity for a bra:
- Breast Development: When a girl’s chest starts to develop, a bra can provide essential support.
- Visibility in Clothing: If the outline of the bust is noticeable in clothing, a bra can offer coverage.
- Physical Discomfort: Feeling discomfort or bouncing during physical activity can signal the need for support.
- Self-Confidence: Wearing a bra can enhance a girl’s confidence and comfort in social situations.
Purpose of Supporting Breasts
Breasts are composed of glands, fat, connective tissues, and fluids, all of which are bound by skin. Everyday activities like walking, running, or exercising can place stress on these delicate structures. A well-fitted bra helps mitigate potential discomfort or injury, making it essential for many women. The right support can also contribute to better posture and overall comfort throughout the day.
The Bra Manufacturing Process
The bra manufacturing process is intricate and requires precision, as improper designs can lead to health issues. Here’s a detailed look at the steps involved:
1. Fabric Selection
The first step in bra manufacturing is selecting appropriate fabrics. Factors to consider include:
- Comfort: Fabrics should be soft and breathable, with cotton blends being popular choices.
- Stretchability: Materials like spandex provide necessary elasticity for comfort and fit.
- Durability: Fabrics must withstand regular wear and laundering, ensuring longevity.
Commonly used materials include:
- Cotton: Soft and breathable, ideal for everyday bras.
- Lycra/Spandex: Offers stretch and shape retention.
- Nylon: Known for its durability and smooth texture.
- Lace: Adds aesthetic appeal, often used in decorative bras.
2. Molding of Bra Cups
The next step involves molding the bra cups. The process includes:
- Foam Selection: Polyurethane foam is often used for its shape-retaining properties.
- Laminating: The foam is laminated with fabric on one or both sides to create the desired finish.
- Molding Process: Using dye-cast molding machines, the foam is shaped under controlled temperature and pressure.
The accuracy of this process is crucial, as it ensures that the cups fit well and provide the necessary support.
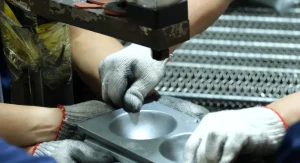
3. Marker Making & Cutting
Marker making involves creating patterns for cutting the fabric. This stage includes:
- Pattern Creation: Markers are designed to optimize fabric usage while accommodating different sizes.
- Cutting Methods: A dye cutter or band knife is typically used. For larger production runs, reciprocating knife cutters may be employed.
Precision in cutting is vital due to the small size of bra patterns. Ensuring proper fabric relaxation and shrinkage control is also essential.
4. Bundling & Separation
Given the small size and similar appearance of bra components, effective bundling is critical. Strategies include:
- Pigeon Hole Storage: Special storage systems help separate different sizes and components, reducing the risk of mixing.
- Organizational Systems: Careful labeling and sorting ensure that each part is easily accessible and correctly matched for assembly.
5. Sewing
The sewing stage involves assembling various components, including cups, wings, and straps. Key points include:
- Bundle Management: Workers take entire bundles for sewing to minimize handling.
- Progressive Bundle System: This method improves efficiency, allowing workers to focus on specific parts without mixing components.
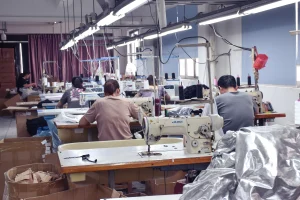
6. Quality Inspection
After sewing, each bra undergoes a thorough quality inspection. This involves:
- Fit Checks: Ensuring that each bra fits properly according to size specifications.
- Material Quality Assessment: Checking for any defects in fabric or stitching.
- Compliance Testing: Ensuring that the bras meet industry safety and health standards.
7. Finishing Touches
Once the bras are sewn, several finishing touches are added:
- Adding Accessories: Decorative elements, labels, and padding may be added during this stage.
- Final Quality Control: Another round of inspection ensures that all finishing touches meet quality standards.
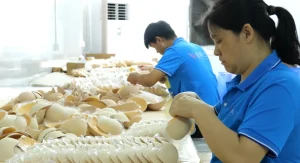
8. Packaging and Distribution
The final stage involves packaging the bras for sale. This includes:
- Attractive Packaging: Packaging should be visually appealing and provide essential product information.
- Efficient Distribution: Bras are distributed to retailers or directly to consumers, with marketing strategies aimed at enhancing visibility.
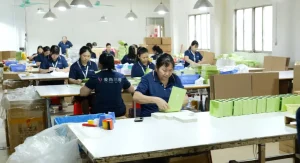
Additional Considerations in Bra Manufacturing
9. Environmental Sustainability
As consumers become more environmentally conscious, manufacturers are increasingly focused on sustainable practices. This includes:
- Material Sourcing: Using eco-friendly materials such as organic cotton or recycled fabrics.
- Waste Reduction: Implementing efficient cutting and production methods to minimize fabric waste.
- Ethical Labor Practices: Ensuring fair labor conditions in manufacturing facilities.
10. Technological Innovations
Advancements in technology have significantly impacted bra manufacturing. Innovations include:
- 3D Printing: This technology allows for custom-fit bras tailored to individual body shapes.
- Smart Fabrics: Incorporating fabrics that can monitor temperature and moisture levels, providing additional comfort.
- Digital Prototyping: Utilizing software to create virtual prototypes, streamlining the design process and reducing time to market.
11. Market Trends and Consumer Preferences
Understanding market trends is vital for manufacturers to stay competitive. Key factors include:
- Customization: Many consumers seek personalized options, including size, style, and fabric choices.
- Inclusivity: Brands are increasingly offering extended size ranges to cater to a more diverse audience.
- Comfort and Functionality: There is a growing demand for bras that combine comfort with performance, such as sports bras designed for active lifestyles.
Conclusion
The bra manufacturing process is a multifaceted journey that involves careful attention to detail from fabric selection to final inspection. Each step is critical in ensuring that the final product is of high quality and meets the needs of consumers. With approximately 18 to 20 operations involved, manufacturers must adapt to style changes and customer preferences while maintaining rigorous standards.
Understanding the intricate processes involved in bra manufacturing helps highlight the importance of each component, from the choice of materials to the final packaging. As the industry evolves, sustainability, technological innovation, and shifting consumer preferences will continue to shape the future of bra production.
By prioritizing quality, comfort, and environmental responsibility, manufacturers can create bras that not only meet the practical needs of wearers but also resonate with their values and lifestyle choices.